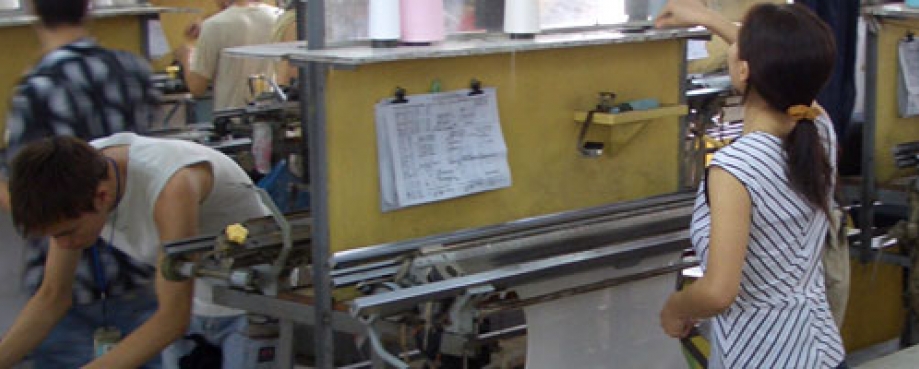
Late last year I visited a sportswear factory in Guangdong, China. With not a speck of dirt in sight, machines gleaming and workers kitted out with all the necessary protective gear, its managers were clearly educated people and rightly proud of their tightly run ship.
Having started out in life as an industrial engineer myself I always feel comfortable in the factory environment and found their pride in their production processes easy to relate to.
And yet I was also struck by the fact that these managers appeared to view their role as being solely concerned with clever technical processes - their workers seemed almost incidental in the production effort. Basic work management tricks to ease the boredom of repetitive tasks, like moving people around the production line or creating production circles, didn't seem to have occurred to them.
It reminded me of Chaplin's brilliant parody of Ford's automated assembly line in the 1936 film ‘Modern Times'.
I didn't get to visit Foxconn in my trip, yet the recent flurry of media reports that have described in grim detail the dehumanising effects of this key Apple supplier's long working hours and militarised discipline, and the social isolation of its workers chime with what we know about too many factories in China.
It may not be a 1930s manufacturing site and it is far from being a sweatshop, as some have said. Yet it is clearly failing the human beings who work for it.
Apple - Foxconn's main, though not its sole customer - finally appears to be making some steps in the right direction in releasing the name of its suppliers and joining the Fair Labor Association. It is important that it also develops a more meaningful, longer-term engagement with the management practices that cause these issues.
But as anyone who knows China will tell you, while the problems that currently bedevil Apple and Foxconn are particularly serious, they are neither new, nor peculiar to these companies.
This is why recent calls from some parts to boycott Apple are a red herring: great for headlines, not so good for tackling the underlying issues across the entire industry. Nor will audits, which continue to typify most buying companies' approaches to ethical trade, drive any lasting change.
All companies sourcing from China must work far harder to meet their responsibilities towards the workers making their products, whether they are in the business of making iconic gadgets or any other product.
Critically, they need to move away from top-down auditing towards developing longer-term solutions that enable workers to start to build constructive dialogue with managers about their problems. In this way workers can become active participants in the process of change rather than passive recipients of limited factory remediation programmes.
Many of our member companies source from China, where we are seeing some encouraging signs that employers are starting to realise the benefits of engaging in constructive dialogue with their employees. For example, our Decent Work Project has demonstrated the progress that is possible when management is willing to listen to workers. New collaborative programmes of work starting this year will also place workers' interests at the heart of strategies for change.
In the meantime, let's hope Apple adopts the same innovative approach to tackling workers' issues that it brings to its product development.
This article was first published on the Guardian Sustainable Business blog on Friday 3 February 2012.