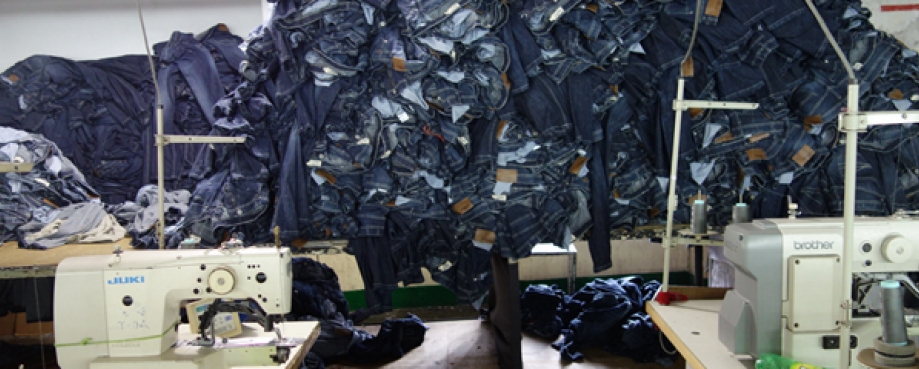
In the morning of April 24th 2013, the Rana Plaza building in Bangladesh – an eight-story building – collapsed, killing more than 1,100 people and injuring over 2000. As well as a bank and several shops, five garment factories were situated in the building. It was the biggest tragedy in a long history of garment factory accidents in Bangladesh and one of the world’s worst industrial disasters.
One year on, the world is in remembrance of the victims and the injured and their families depending on them, that still suffer from the consequences of this terrible tragedy on a daily basis. The process of compensation of the victims is in a critical stage as we pass the one year anniversary.
At the same time, efforts to avoid another Rana Plaza from ever happening again were initiated in the past year, and the Accord on Fire and Building Safety in Bangladesh is one of those. The Accord is a ground-breaking worker safety initiative of which 166 apparel brands and retailers are now signatories, along with two global union federations, eight Bangladeshi garment workers’ unions and union bodies, and four international labour rights organizations, participating as witness signatories.
Elements of the Accord’s key characteristics include its legally binding nature; its independent inspection program; its high degree of transparency to both the public and to workers; the brands’ commitment to ensure financial capacity for renovations and to reward safe factories with ongoing business; and a strong worker participation and training programme. The design of the Accord reflects the understanding that protection of worker safety is impossible without meaningful worker empowerment. The Accord contains a series of provisions that ensure not just that workers can participate in the program, but that workers can influence the program, both in terms of what happens on the factory floor and at the highest levels of Accord decision-making.
These provisions sound promising but what has the Accord achieved almost one year after its inception on May 15 2013? How far has the Accord progressed in its goal to enable a working environment in which no worker needs to fear fires, building collapses, or other accidents that could be prevented with reasonable health and safety measures?
It’s important to note that the Accord has grown to become a massive undertaking. Accord brand signatory membership increased dramatically from around 40 brands and retailers in May 2013 to 166 by the end of April 2014, covering more than 1600 factories employing approximately two million workers. And the Accord is still welcoming new signatories on a weekly basis. Whereas the first 6 months was dedicated to developing an implementation plan, recruitment of the Accord team and setting up offices in Dhaka and Amsterdam, in November 2013 ten pilot factories were the first to be inspected. Their inspection reports and Corrective Action Plans are now online.
In February this year, the inspection program started in full swing, aiming to have 1500 factories inspected for fire, electrical and structural safety by October 2014. More than 300 factories have been inspected so far. The Accord has now approximately 110 externally contracted engineers and technical experts working in the field, inspecting approximately 45 factories per week.
The Accord inspections are identifying safety risks in all of the factories. Some of them can be easily corrected, such as reducing weight loads and properly connecting and sealing electrical wires and keeping wires and circuits free of dust. Other findings and safety requirements involve more substantial renovations, such as installing fire doors, automated smoke detectors and fire alarm systems, sprinkler systems and strengthening of columns.
So far, 8 of the structural inspections by the Accord have resulted in ‘critical findings’, leading the inspection team to recommend temporary suspension of (parts of) the production in the factories. Such temporary evacuation would allow for more in-depth tests, weight and load removal from the building, or immediate strengthening measures. Decisions to temporarily suspend production are not taken lightly, but they are taken for a good reason, because the factories are unsafe and we want to avoid another building collapse. It is a clear area where the Accord is fulfilling its core mission, which is getting workers out of the most dangerous factories until they are made safe. An important safeguard to avoid loss of jobs is the Accord’s provision that workers’ employment relationships and wages shall be maintained for 6 months during renovations.
The challenges ahead for the Accord are finalising and implementing corrective actions plans, monitoring the commitment of brands to meet their obligations under the Accord and ensuring worker participation and the development of effective Occupational Health and Safety Committees. The Accord’s strength lies in part in its focussed approach, which is challenging enough in itself, but it means we must be humble and realise that there is a lot more to do to improve all labour conditions in the Bangladeshi garment industry.