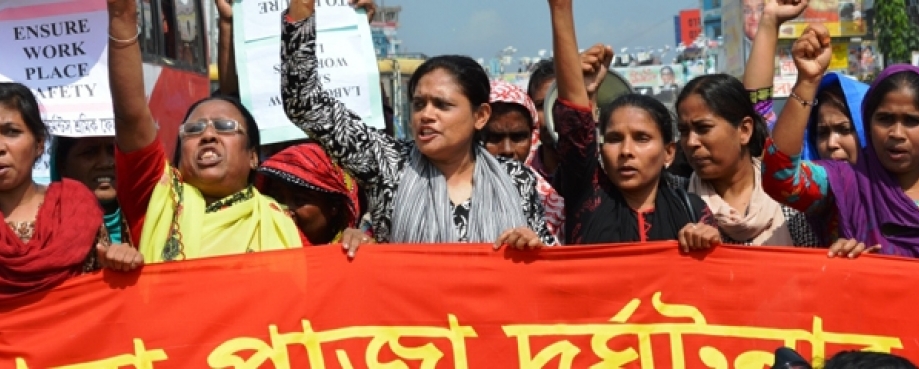
24 April 2013 is a date that is imprinted in global memory. It was the day that more than 1,100 Bangladeshi workers lost their lives when Rana Plaza collapsed. As we mark the one year anniversary of this terrible day, our thoughts are with all those that suffered loss and injury in this horrific tragedy.
We commend those retailers and brands that have paid compensation in line with the established and International Labour Organisation (ILO)-backed Rana Plaza Donors Trust Fund. But we urgently call on all brands and retailers that sourced from Rana Plaza to also step up and do the right thing. It is unacceptable that many workers and their families have had to wait a year to even start receiving compensation payments.
The collapse of this multi-storey, multi-purpose building put Bangladesh’s commercially successful garment sector in the public spotlight. It shone a very bright light on the chronic health and safety issues that are endemic to the sector and prompted challenging questions to be asked of the Bangladesh government, local industry and international retailers and brands. So what has changed during the past year?
International focus on improving factory safety
The international community heeded the call for change, establishing three important frameworks. The ILO worked with the Bangladesh government and employers’ and workers’ representatives to produce a national action plan on fire and building safety. The Accord on Fire and Building Safety in Bangladesh brings together more than 160 international brands with global and local trade unions, supported by NGOs. ETI has publicly championed the Accord since its inception because of the involvement of global trade unions, and many of our company members were amongst its first signatories. The third international framework is the Alliance for Bangladesh Worker Safety, which brings together 26 North American apparel brands and trade associations.
These international initiatives recognised an urgent need to identify Bangladesh’s most unsafe garment factories and take immediate action to protect worker safety. To date, more than 700 factories producing garments for Accord and Alliance members have received electrical, fire safety and structural inspections. These have resulted in immediate actions prioritising worker safety and many factories have already begun to implement factory repairs.
We recognise that the Accord and the Alliance have made progress, but there is a need for increased momentum. Unsafe factories must be urgently identified and repaired, so that people can enjoy safe working conditions. It is an incredibly complex environment involving many stakeholders, but this cannot impede progress.
Our efforts to amplify workers’ voices
It is vitally important that workers are central to all efforts to drive industry-wide change. Improvements on occupational safety and health will not be sustained unless workers are able to exercise their right to freedom of association and to bargain collectively over the conditions of work. While the past year has witnessed registration of new trade unions in Bangladesh’s garment sector, this represents only a tiny fraction of a workforce of more than 4 million. Despite these important measures, it remains extremely difficult for workers to exercise their fundamental rights in Bangladesh.
ETI has launched a three year project with our Danish counterpart DIEH, funded by the Danish government. Drawing on the collective expertise and knowledge of our members and local stakeholders, we are promoting a model of social dialogue for the Bangladesh garment sector. This project complements the Accord, the Alliance and the Bangladesh government and ILO-backed national action plan.
ETI Director Peter McAllister said: “Our focus is on building supplier capacity and establishing robust mechanisms so that workers can better exercise their rights and play a meaningful role in driving sector-wide change.”
Alongside their support for the international agreements, ETI company members also undertook their own efforts during the past year, putting in place a number of changes that address health and safety issues. They conducted more than 1,200 safety inspections of Bangladesh supplier factories (in addition to Accord and Alliance inspections), strengthened in-country capacity to deal with any issues that arise and invested in health and safety training for Bangladeshi managers and workers. A number have also recognised the need to support the creation of freely elected workers’ representative committees.
We take this opportunity to highlight the plight of garment factory workers in other parts of Asia including China, Pakistan and Cambodia. Workers in these countries also face health and safety issues as part of their daily experience. Whatever we learn from Bangladesh must be shared with other countries and sectors, so that the widest number of workers possible can benefit.
The international community has responded to the devastating events of 24 April 2013 and we are seeing the first signs of change. But we will only truly do justice to the memory of those lives lost by fully delivering on the promises made to Bangladeshi garment workers.