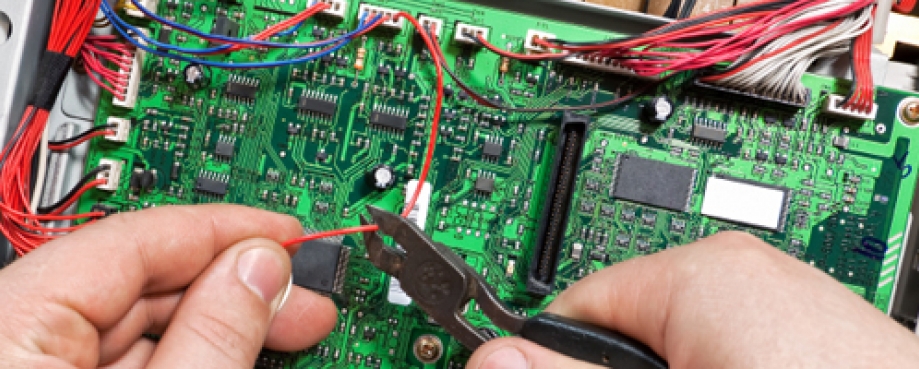
Abi Rushton looks at the parallels between the electronics industry and fast fashion, and asks if it's making the same blunders in addressing working conditions as the fashion industry, or learning from its mistakes?
As new electronic gadgets come to market with increasing frequency and updated models are released almost annually, the electronics industry is coming under increased scrutiny about where and how these products are made.
2010 saw Apple come under increasing examination about the factories making their iPhones, iPods and iBooks. Although neither Foxconn nor any of the other factories in question make exclusively for Apple, none of the other electronics companies using these sites have received the same scrutiny.
The media coverage is nothing new, as many iconic clothing brands can attest - their names have been splashed across the newspapers while less high profile companies go unreported. This is the price that Apple has to pay for becoming the world's leading electronics company.
In response to this Apple recently published its Supplier Responsibility 2011 Progress Report. The title itself is interesting. The ethical trade movement has tended to push responsibility for labour standards in international supply chains on to the consumer facing brands. The title suggests that Apple are trying to redress this, and demonstrate that it is the suppliers' responsibility to ensure decent working conditions for workers in their own premises.
However the content of the report speaks of holding suppliers accountable to Apple's own standards and codes of conduct, rather than stressing the existence of local labour standards which meet international norms. This seems to contradict the empowerment of suppliers hinted at in the title.
Supplier responsibility is the ultimate goal of any western retailer faced with global supply chains. Lack of local capacity to enforce these standards and corrupt officials makes this easier said than done. Given these difficulties Apple should be congratulated on uncovering the cases of underage labour, record falsification and attempted bribery that it cites in its progress report. These are not easy issues to acknowledge, and with the limitations of global auditing programmes well documented, Apple's willingness to talk about them deserves even more acknowledgement.
What is less clear is how the underlying systemic issues of corruption, increasing consumer demand and resultant pressure on lead-times are being tackled to bring about sustained improvements for workers. These issues are well documented in clothing supply chains and have been addressed with varying degrees of success. As the electronics industry becomes more and more fashion-led, surely there are opportunities to learn from fashion itself?
Industry groups such as EICC (Electronic Industry Citizenship Coalition), which Apple is a member of, serve as great forums to collaborate and speak with one voice to the supply chain, but working across industries to improve labour standards could save a lot of time and stop similar mistakes being made.