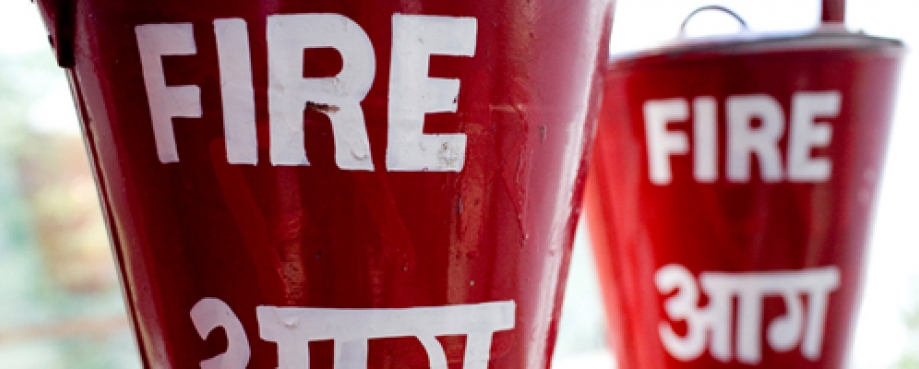
Stuart Bell, Director of Policy at Ergon Associates, looks at some of the shortcomings of conventional audits as a tool and how companies are increasingly taking a different tack.
As ETI's corporate members prepare to submit their annual reports, it's worth reflecting on what they tell us about the state of ethical auditing, and to consider other ways of pursuing ethical trade. Our analysis of ETI members' audit findings provides ample evidence of the limitations of relying solely on audits as a means of identifying and rectifying labour abuses. They reveal a predominance of health and safety issues, followed by breaches on wages and working hours, but freedom of association and discrimination violations lag far behind. Relying on audits alone would suggest that these two issues are not problematic for workers. This is clearly nonsense. While audits are useful for spotting 'material' infractions, other issues, often reliant on capturing worker perspectives, slip under the audit radar.
Superficial issues
And the non-compliances that are spotted by auditors are often not addressing the real problem. For instance, ETI members pursue a large number of improvement actions on wage non-compliances. But the majority of these actions are about provision of wage slips or adequate payment records - they seldom address how much money ends up in a worker's pocket, as performing a living wage calculation is rarely part of an auditor's brief.
Symptoms not causes
A second problem is that audits identify the symptoms of problems, but infrequently address the causes. Conventional inspections may show up a locked fire escape, but they don't say anything about why factory managers felt that this was an acceptable practice. Equally, audits may reveal shortcomings in record-keeping, but won't suggest the systemic improvements needed to upgrade either administrative or HR processes. If we are interested in continuous improvement, a tick-box, compliance-based approach can only take us so far.
What sustains standards?
So how can companies shift from measuring outcomes to improving the key processes within suppliers that allow poor working conditions to persist? One way of thinking about this is to look at the factors that maintain standards in the reputable companies we all admire. Day-to-day standards are almost certainly not reliant on the threat of third party inspections. More likely, they are maintained by a combination of formal and informal systems and expectations. An effective regulatory background is certainly important but beyond that, high standards rely on values and leadership from the top, embedded through policies and procedures, whether written or unwritten, applicable to all relevant employees.
Accountability not inspections
Standards also rely on mechanisms for feedback and accountability. Recognised trade unions provide one important channel for holding management to account, but an environment in which employee feedback is encouraged is equally important. In sum, good practice is established and nurtured more by the effective management of human resources and industrial relations, supported by internal communication structures, than by external assessment of workplace conditions.
Process is the key
Already a number of ETI members and other organisations have realized that effective HR processes can be a key to improved workplace standards and are working with individual suppliers on these issues. However, such an approach is not yet mainstream, and companies and their auditors could be doing much more to develop ways of assuring themselves about the quality of suppliers' HR processes.
If they did so, they would not be alone. The International Finance Corporation (IFC), for example, the private sector arm of the World Bank, has a series of 'performance standards' including around labour, which it expects its borrowers and investee clients to follow. This emphasises the robustness of HR policies and processes and policies rather than expecting audit-based compliance with a code of conduct. Similarly, while also requiring compliance with labour standards, SA8000 now has a section that requires the embedding of HR processes.
Ruggie framework
The importance of process in supporting higher standards is also emphasized by the draft new UN principles on business and human rights, developed by John Ruggie's team. This is set to become the main international reference point for how businesses should tackle human rights, including labour rights.
In Ruggie's draft 'Protect, Respect and Remedy' framework, various responsibilities are placed on businesses, many of which relate to the processes they should adopt to safeguard rights. Under the 'Respect' pillar, directed specifically at businesses, they should ensure they have appropriate policies, due diligence and risk assessment processes and remediation strategies in order to ensure respect for human rights and labour standards. It is noteworthy that this applies both to their own operations and their supply chains.
Ruggie's 'Remedy' pillar spells out the responsibilities that the State and businesses share to provide avenues through which workers can air grievances. Setting up effective enterprise-level complaints mechanisms is one area where ETI member companies have struggled to make progress in recent years. But if one failure of conventional audits is their inability to capture how workers feel about their conditions, then implementing grievance mechanisms can only be a positive step, and one that will strengthen HR practices and internal accountability.
Auditing is not going to go away, but if it is not complemented, and increasingly supplanted, by activities that support sustainable and accountable human resource practices within suppliers, progress towards ethical supply chains will continue to be painfully slow.