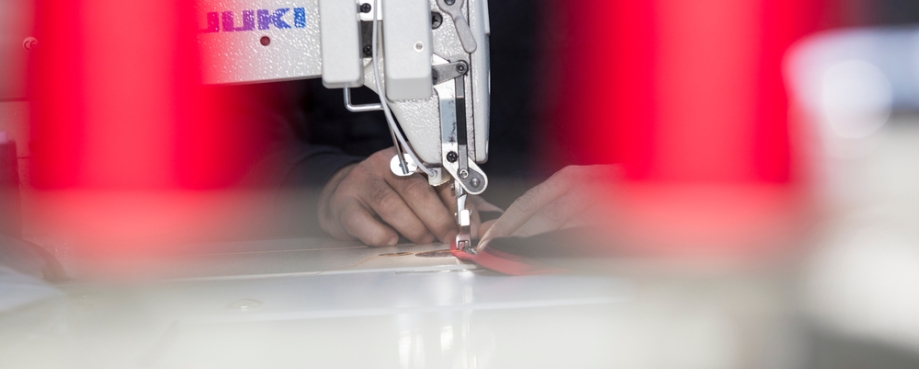
Over the course of seven-weeks in Türkiye, I had the opportunity to speak with over 40 stakeholders across the country’s apparel and textile sector. From suppliers, and export associations, to trade union and NGO representatives, each offered insight into the challenges faced by local industry and the added complexity brands’ purchasing practices can bring.
Türkiye has long been a global leader in textiles, known for its design expertise and high-quality production. However, like their counterparts in India and Bangladesh, Turkish suppliers face significant challenges due to purchasing practices employed by sourcing brands. What sets Türkiye apart is that, in addition to the typical challenges faced by apparel-producing countries, it contends with economic difficulties and a trend of brands moving production elsewhere. This has created particularly tough conditions for suppliers and their workers.
Challenges for manufacturers
Turkish manufacturers often refer to Türkiye as the "sampling room of the world." It’s a reference made in frustration at the frequent requests by brands to produce samples while mass production is shifted to cheaper locations. This practice strains businesses that invest heavily in prototypes without securing orders.
Manufacturers also face immense pressure with some brands prioritising price over partnerships. One common phenomenon is “ghosting,” where brands show initial interest and then disappear after the sampling phase. One supplier shared their experience:
“After investing substantial resources to produce 37 samples, we only received 11 back after two years, and there were no orders.”
Delays in feedback and sudden unrealistic turnaround requests further complicate relationships. Suppliers wait for months without updates, only to face last-minute demands that make sustainable collaboration nearly impossible. One supplier noted:
“Brands come in saying they want a partnership, we make agreements, but then leave me huge amounts of stock that they do not use, and I’m left to absorb the costs. And there’s nothing I can do about it.”
All these issues highlight the power imbalance between brands and suppliers. “Their will is law, and we have to do what they say,” one supplier remarked, pointing to the inequity in their business relationship.
Challenges for trade unions
Establishing a trade union in Türkiye’s A&T sector is a complex process. Unions must first represent at least 1% of the workforce and then gain support from 50% of employees in the factories they aim to organise. This process is further complicated by union-busting tactics from manufacturers and government bodies.
Adding to these challenges, trade unions highlighted concerns about migration-related workforce dynamics in Türkiye. While many migrant workers contribute significantly to the textile industry, their employment often comes with lower wages, fewer rights, and an increased risk of exploitation. Factors such as informality, illegal employment, and fear of reprisals make these workers particularly vulnerable. This situation requires careful attention to ensure fair treatment and safeguard workers’ rights.
Trade union representatives also shared that textile workers are among the lowest paid in the country, facing long working hours and health and safety concerns. This situation is further exacerbated by a lack of support from brands, who prioritise cost savings over sustainable practices. One union leader emphasised,
“Suppliers are left with little margins. If costs increase due to rising wages or inflation, customers should adjust their prices too, but it shouldn’t fall solely on suppliers to cut their margins.”
Another significant challenge is the perception of unions as enemies by suppliers, stemming from misunderstandings about their role. A lack of awareness about unions’ efforts to secure fair wages and working conditions breeds mistrust and makes cooperation difficult.
Despite these hurdles, unions remain committed to engaging with manufacturers to demonstrate the benefits of fair labour practices. They believe transparent communication and active collaboration can lead to positive outcomes that protect workers' rights and enhance industry sustainability.
Brand perspectives on sourcing from Türkiye
Brand representatives have pointed out that Türkiye's economic challenges have increased product costs, making it a more expensive sourcing destination. However, during panel discussions at the Istanbul Apparel Conference, organised by Türkiye Giyim Sanayicileri Derneği, brands like Ralph Lauren and Faherty highlighted Türkiye's consistent quality and strong supplier relationships as key reasons for continuing to source from the region. At the same time, concerns around freedom of association have grown, likely influenced by brands reducing order volumes or withdrawing from Türkiye. These points have also been confirmed by trade union representatives.
The relationship between manufacturers and trade unions
The relationship between manufacturers and trade unions is a highly sensitive issue in Türkiye’s A&T sector. While unions are vital for advocating workers' rights, many manufacturers view them sceptically due to concerns about disruptions to operations or increased demands. This mistrust often stems from past negative experiences and a lack of understanding of the benefits unions can offer.
For example, one supplier agreed to unionisation at a brand’s insistence, but when worker representatives demanded higher wages, the brand refused to adjust pricing. The supplier had to close two factories, leaving workers unemployed. This underscores a major failure: brands push for union presence but do not provide long-term support, resulting in severe consequences for both suppliers and workers.
Building constructive relationships between manufacturers and trade unions is crucial for sector stability. Successful partnerships rely on mutual trust, clear communication, and shared goals. Brands must recognise that supporting unions involves more than meeting ethical standards; it requires active, sustained engagement. Manufacturers should be equipped with the resources to navigate unionisation, and brands should facilitate this process.
“Some brands insist on union presence without understanding the Turkish context, which can worsen conditions for both suppliers and workers,” said one supplier.
How can progress be made?
Collaboration between unions and suppliers is vital. Türkiye’s strengths in design, innovation, and quality production, coupled with the global push for sustainability, present opportunities for growth. With regulations like the CSDDD driving transformation, stakeholders must unite to turn challenges into progress.
Most importantly, to ensure a sustainable and equitable industry, brands must reform their purchasing practices. As one supplier noted, “If we live, they live,” highlighting that the prosperity of the entire supply chain depends on shared responsibility. Brands need to commit to fair compensation, transparency, and genuine partnerships that go beyond lip service. Only by fostering strong, mutually supportive relationships can partnerships thrive, driving a future where workers are treated fairly, and the industry as a whole is resilient and sustainable.