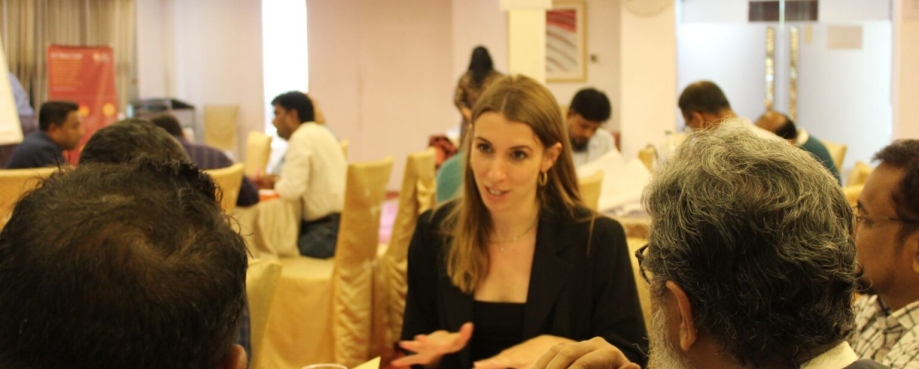
This summer, I spent 10 weeks in India and Bangladesh, engaging with over 180 stakeholders across the textile and garment industry on the topic of responsible purchasing practices. This included group discussions with 83 suppliers, 33 trade union leaders, 33 brand representatives, and 35 export association members.
My aim was to gain a deeper understanding of local perspectives on purchasing challenges and share insights on common framework for responsible purchasing practices (CFRPP) and the efforts of the working group in the learning and implementation community (LIC). These extensive interactions shed light on the pressing challenges of current purchasing practices, revealing critical issues that directly affect workers’ lives and the sustainability of the textile industry.
Here’s what I learnt:
Many stakeholders are still unfamiliar with the concept of responsible purchasing practices
From a supplier’s perspective, the burden of responsibility and risk largely falls on them, and the idea of sharing risks is still relatively new. Of the 83 suppliers I spoke to, 97% mentioned that their customers (brands) never asked them if the way they currently work is working for them. Despite strong interest in the topic and a clear desire for broader discussions among brand representatives, suppliers, export association members, and trade union leaders, many expressed that they do not feel adequately heard or empowered to voice their concerns to their customers (brands).
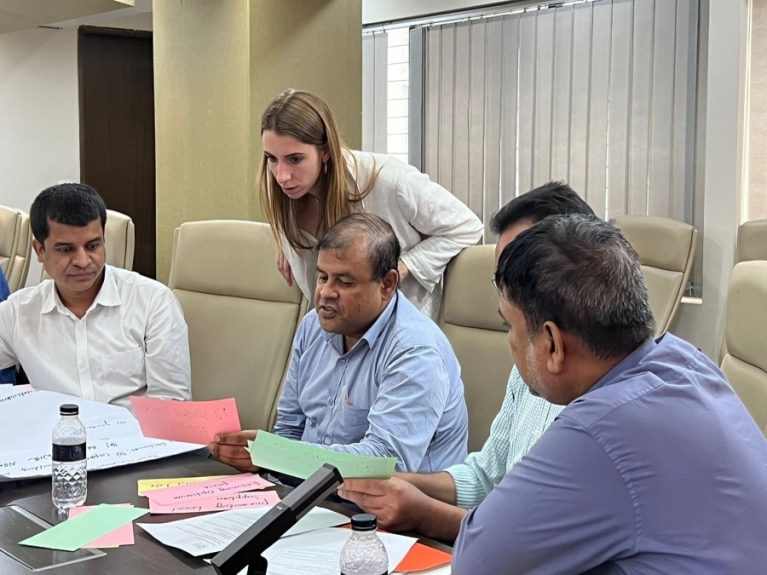
There are four key challenges within current purchasing practices:
Pricing
One of the most urgent and frequently mentioned issues is the widespread use of unsustainable pricing practices. Suppliers repeatedly raised concerns that they are often offered prices that do not cover their production costs. As one supplier said, "How are we supposed to maintain quality or pay our workers fairly when we’re forced to accept these prices?" The problem of unsustainable pricing was echoed by trade union leaders and brand representatives, as it remains a common issue in the garment industry. A brand representative mentioned, “It is often still a choice between hitting target prices vs. sustainability,” while a trade union leader noted, "Brands' irrational costing strategies fail to meet actual needs, ultimately harming workers the most."
“We get a standard open costing template that doesn’t account for environmental or social costs. These costs are there, but if we can’t reflect them, it will ultimately impact other budget lines. If we continue to use these, brands should include every small cost, including sustainability, in the open costing template—what’s the point otherwise?”
This problem is compounded by brands reducing prices after shipment if the goods don’t perform well in stores, asking for discounts after products are already made, or even cancelling orders when they are already in production or finished, leaving suppliers to bear the financial loss. Open costing models are used throughout the industry, but many raised concerns. “It is turning into a buyers' market, when it used to be a sellers' market. If it were fair, buyers should also provide an open costing model,” one supplier said. Suppliers who already work with open costing models mentioned that open costing often fails to account for sustainability costs, making it nearly impossible for suppliers to invest in improvements while keeping their businesses afloat. “We get a standard open costing template that doesn’t account for environmental or social costs. These costs are there, but if we can’t reflect them, it will ultimately impact other budget lines. If we continue to use these, brands should include every small cost, including sustainability, in the open costing template—what’s the point otherwise?”
Auditing
"To the suppliers, it feels like a marketing strategy. All this talk of sustainability on social and environmental issues is just adding extra points in their audits and checks because they want to report on ESG and make themselves look good—but they don’t consider the consequences of what all these checks and extra audits mean."
Another challenge frequently raised was the overwhelming burden of audits. Many suppliers face numerous, often redundant audits—even if they do not have orders with the brands at the time. One supplier described this issue: "We spend so much time on audits that it takes away from running the business. Sometimes, these audits come from companies that don’t even place orders with us." Another supplier mentioned: "To the suppliers, it feels like a marketing strategy. All this talk of sustainability on social and environmental issues is just adding extra points in their audits and checks because they want to report on ESG and make themselves look good—but they don’t consider the consequences of what all these checks and extra audits mean." The lack of a standardised audit process adds unnecessary complexity and costs for suppliers, leading to inefficiency without real value. "There is a need for uniform global compliance standards," a trade union leader said, as these audit requirements not only fatigue suppliers but also impact workers, with increased time spent on interviews and surveys, causing stress.
Consistency & lead times
"We’re constantly racing against impossible deadlines, and if we don’t meet them, we lose the business."
Tight and unrealistic lead times remain a common concern. Over the years, lead times have shrunk dramatically—from 90 days to as little as 30. One supplier said, "We’re constantly racing against impossible deadlines, and if we don’t meet them, we lose the business." These compressed schedules often come at the expense of quality and worker well-being, yet brands rarely adjust their buying timelines to accommodate on-the-ground realities. To make matters worse, last-minute order changes disrupt production, further straining the supply chain. Trade union leaders and export association members raised concerns about the lack of consistency in orders. "One month, suppliers are overburdened with orders, and workers have to work overtime and long hours while suppliers hire non-contractual workers. The next few months, they let people go because there is no business". Brands and suppliers should work together to provide a consistent workflow that benefits everyone. In an ideal world, suppliers should be able to communicate that they cannot meet a deadline. But most do not, as brands will move to different suppliers who can. For those who do, they get responses like, “Why are you not being collaborative?” or “You’re being difficult; we need to get this done.”
Eroding partnerships
This all leads to perhaps the most concerning trend: the erosion of partnerships between brands and suppliers. Many suppliers feel they can no longer negotiate or raise concerns without risking the loss of business. As one supplier put it, "It used to be a partnership. Now, if we don’t agree to their terms, they take their business elsewhere." This power imbalance leaves suppliers vulnerable, especially when brands cancel orders after production or use external factors like political instability to negotiate lower prices. When unrest broke out in Bangladesh, within a few days Indian suppliers were contacted to move production from Bangladesh. An Indian supplier mentioned: “Of course I’m happy with these orders, but I know for a fact this won’t last. The moment Bangladesh gets back to normal, they’ll move back—is this a reflection of a partnership?”
"This will impact us all. If we do not start making this industry more sustainable and attractive, brands will be impacted too."
There are live challenges for the garment industry which is likely to suffer if they persist. Many mentioned that finding workers is becoming increasingly difficult. “The young generation does not want to work in this industry anymore, and can we blame them?” one said, citing long working hours, stressful work, and wages that aren’t always attractive. "This will impact us all. If we do not start making this industry more sustainable and attractive, brands will be impacted too. The garment industry is a people business, and we need skilled people to produce our products—a sustainable working environment will ultimately lead to better business for everyone."
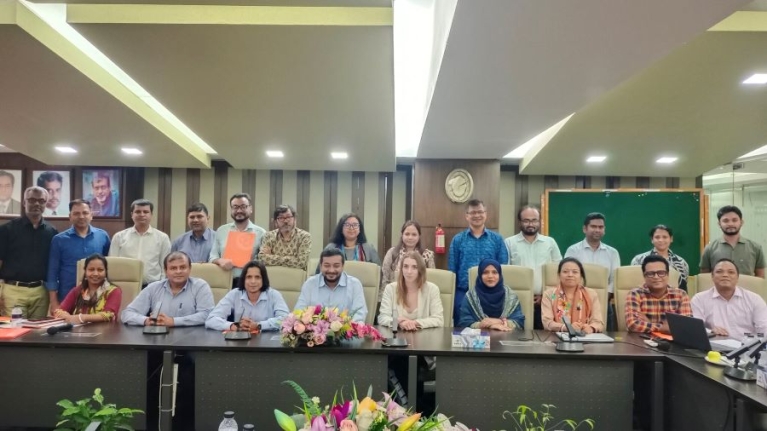
Current purchasing practices have profound adverse impacts on workers
Delayed wage payments, excessive working hours, and insufficient benefits are some of the dire consequences that arise when suppliers are squeezed by unfair practices. Trade unions emphasised that the strain on factory management affects worker morale and stress, creating a cycle of dissatisfaction and instability.
A trade union leader shared, “Workers are the first to suffer when there’s financial strain on factories. They’re asked to work longer hours, or they’re let go with little notice when orders dry up.”
This instability not only affects the livelihoods of workers but also has broader implications for the social and economic fabric of the communities in which these factories operate.
At the same time, this has wider implications for the industry. When speaking to different countries, they all say the same thing: the younger generation is not interested in working in this industry anymore. This means it is becoming more difficult to find workers, and if we continue to exploit the industry in this way, there will be wider consequences for the entire sector. The immediate solution is to rely on migrant workers, who often have fewer rights and receive lower wages.
Multistakeholder action is critical for positive change
Addressing these challenges requires coordinated efforts from all industry players. Each stakeholder group provided recommendations for others to work collaboratively towards responsible purchasing practices:
- Trade unions
Unions must strengthen ties with factory management to advocate for fair wages and working conditions. They should also raise awareness of workers' rights and push for greater involvement in RPP policy discussions, ensuring workers’ voices are represented when negotiating with buyers. - Brands
Brands need to establish fair pricing strategies that cover production costs and sustainability efforts. Simplifying audit requirements would reduce the burden on suppliers, allowing them to focus on improving operations. Brands should also respect realistic lead times and avoid last-minute order changes that cause unnecessary strain on the supply chain. Finally, rebuilding trust with suppliers and fostering long-term partnerships based on mutual respect is essential to creating a more equitable industry. - Suppliers
Suppliers are encouraged to join capacity-building initiatives to strengthen their bargaining power. Increased transparency, particularly in areas affecting workers and the environment, is crucial for building trust with buyers. Providing training for mid-management at the factory level is also essential, as gaps in sustainability understanding persist between higher and mid-management teams. Embracing new technologies, such as 3D sampling, can enhance efficiency and competitiveness. Ultimately, suppliers should refuse to accept prices that do not cover production costs. - Export associations
Export associations should focus on educating suppliers to broaden their understanding of responsible purchasing practices. With their extensive reach, they have the platform to share knowledge with a wider supplier base, sharing best practices, encouraging interactions and collective problem solving among members. Additionally, associations can play a key role in lobbying for fairer practices and stronger labour always, working alongside trade unions. By collaborating with MSIs, they can help promote wider adaptation of responsible practices while collectively addressing issues with buyers. - Multistakeholder initiatives (MSIs)
MSIs can facilitate dialogue between buyers, trade unions, export associations and suppliers, helping to address ongoing challenges, being the bridge. They can also provide the necessary training and resources for stakeholders to increase awareness of RPP, and advocate for ethical practices throughout the supply chain.
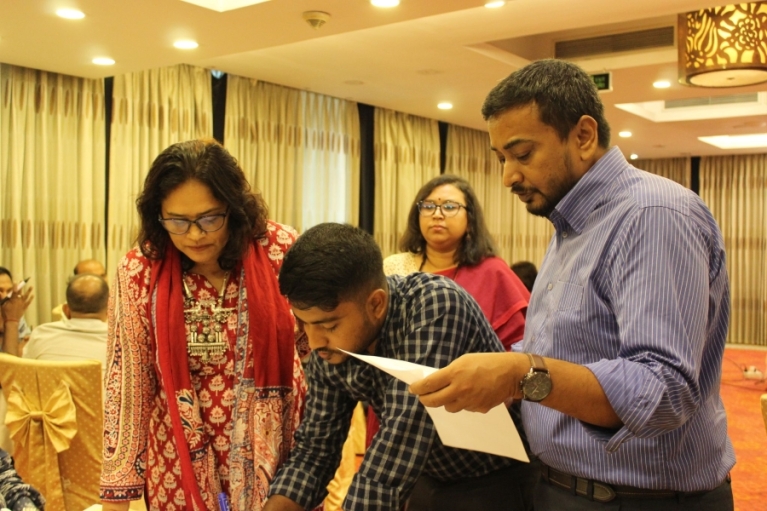
My visits confirmed that while responsible purchasing practices are increasingly recognized as essential, significant gaps remain between rhetoric and reality. Challenges faced by suppliers are complex but solvable with collaborative efforts. MSIs like ETI play a crucial role in facilitating these conversations. Trade unions can enhance discussions with worker perspectives, and suppliers and export associations should focus on fair wages and production costs. Brands must be accountable for responsible purchasing practices, pay fair prices, and maintain realistic lead times.
ETI will continue its work on responsible purchasing practices, and as a follow-up to the awareness-raising sessions on RPP in production countries, will aim to start roundtables in the new year. At the same time, ETI, in collaboration with the working group on RPP, has been working on an accountability framework that will offer guidance to hold brands and retailers accountable for responsible purchasing practices, which is now open for consultation.
While regulations like the CSDDD will aid this transformation, brands must lead the change. By fostering equitable partnerships, respecting timelines, and adopting sustainable pricing strategies, the industry can create a more transparent and just future where workers benefit from their rights and decent working conditions.