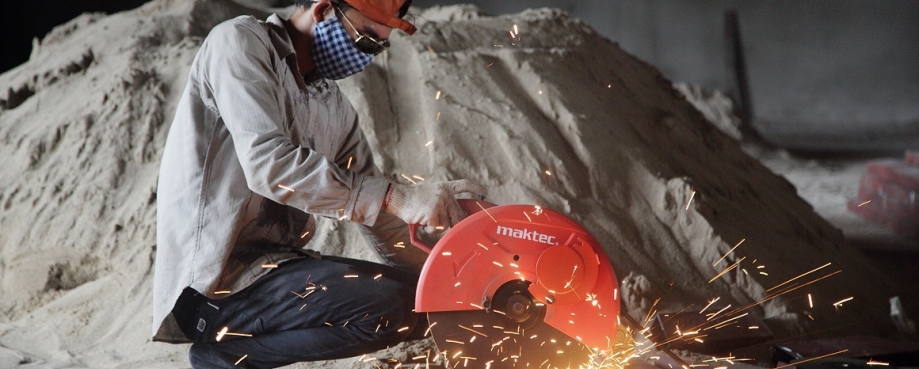
Stirling Smith, ETI trainer and blogger, tackles a common myth around health and safety at work and managing risk.
I was training some managers recently and one of them said, "But the workers don't wear the personal protective equipment".
This particular discussion took place in Vietnam, and in a garment factory, but it could have taken place anywhere in the world. It's a common statement.
So, this blog is going to deal with a widespread misconception about safety and health at work: the theory that the problem is careless workers.
Industrial Accident Prevention: A Scientific Approach
The careless worker theory dates to the work of an American psychologist, Herbert William Heinrich (1881-1962) who published the book, Industrial Accident Prevention: A Scientific Approach in 1931. This was based on an analysis of thousands of accident reports. Based on these reports he hypothesised that accidents were caused by "unsafe acts" by workers. You can read more here.
This has led to a whole branch of the health and safety industry dedicated to ways of making workers “improve” their behaviour.
The problem with this approach is that it does not deal with the root causes of accidents and disease at work. As I have blogged before, the proper approach is to follow the "hierarchy of control".
This is going to get a bit technical – but never fear, I have been explaining safety jargon for 40 years. Hang on to your hats.
We need to start off by defining two key concepts: hazard and risk.
Hazard is anything present in the workplace that has the potential to cause harm to workers, either a work accident or an occupational disease. For example, a machine with the potential to injure – from a sewing machine to a huge saw cutting sandstone in Rajasthan. Or a chemical or dust – like the dust created by that saw cutting stone.
We cannot change the hazard. The chemical is the same anywhere in the world.
What we CAN change is the risk, because that is the chance or probability that a hazard will actually result in injury or illness of a worker. We can reduce the risk through control measures.
The hierarchy of control
The hierarchy of control approach starts off by asking whether it is possible to eliminate the process that is causing the hazard. If not, then we need to reduce the risk that the hazard will harm the worker.
We might, for example, substitute a less hazardous chemical for a more toxic one. We might put in engineering controls to take away harmful chemicals so the worker does not have to come into contact with it. We might put needle guards on sewing machines. That reduces the risk.
If none of these approaches are possible, then we might need to consider administrative controls.
Let's say you are working in an extremely hot environment. Rather than ask one worker to do an eight-hour shift, you might get four workers to do two-hour shifts in the very hot atmosphere, and the rest of their shift in a cool one. It does not change the heat, you cannot change the hazard, remember? But it reduces the risk that working for long hours in heat will have on the worker – heat stroke is a killer.
Or take spraying pesticides. Asking workers who are spraying pesticides to wear personal protective equipment in a really humid environment, like Assam, is quite impractical. What you can do is rotate the work, to reduce the overall exposure. You could try to change the pesticide, but if you cannot do that, reduce the risk by rotating workers. Their pesticide dose is thereby reduced.
There is a lot of rubbish PPE out there
Only if you have tried everything else, should you start to consider PPE. Then you must make sure that the PPE is fit for purpose.
Does it keep out the dust or the chemical?
And you need to make sure that the PPE is easily accessible to workers, they don't have to walk a long way to the stores and then fill in multiple forms, and show the old damaged PPE before they receive new stuff.
All these controls result in PPE not being used.
When you do an audit, go to the stores and find the PPE section. Check the manufacturer’s specifications. Try throwing a helmet on the floor to see if it cracks. There is a lot of rubbish PPE out there.
Some years ago, Coal India Ltd, gave out self-rescuers to miners that were fakes, made in China. A self-rescuer is what you put on in a mine when there is a fire, and it stops you dying from carbon monoxide poisoning. If it's a fake, then you die. If people are willing to make and sell and buy such equipment, to make a buck, then they won't hesitate to pass off inadequate dust masks. By the way, it was the trade union that blew the whistle on that scandal.
Involve the end users
All PPE should be checked and double checked with the workers, to see if it really is comfortable and suitable to use. After all, they are the end users.
Of course, if you have trade union safety representatives, they can help choose the PPE.
Management needs to set an example by always wearing the same PPE if they visit the shop floor, even for 10 minutes. And there does need to be a proper education for workers explaining the reasons for wearing it.
If after all this, workers still do not wear PPE, then maybe you have grounds for saying "but the workers don't wear the personal protective equipment".
One more question to ask Mr Root Cause. “What about workers who remove guards?”
Mr Root Cause replies: “They do it because it slows them down. Because they are on piece rate payment or have an unreasonably high target to meet. Investigate that before blaming workers.”
Back to our friend Mr Heinrich; the accident reports he analysed back in the 1930s were written by supervisors and managers. Naturally, they blamed the workers rather than the management of the factory.
Ultimately, the control of safety and health at work rests in the hands of management.
The problem is not careless workers, the problem is careless managers.