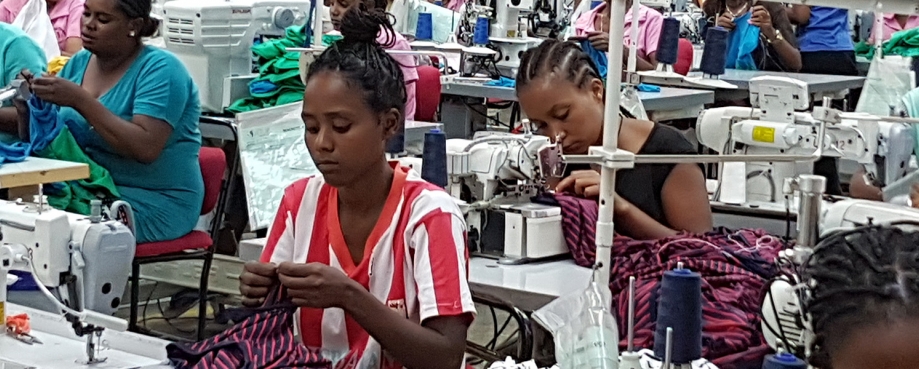
Despite Ethiopia being one of the most fertile and beautiful areas of Africa with a rich history at the root of the human story, it’s recent past has been plagued with droughts, famine, armed conflict and a large refugee population. Despite these devastating circumstances, there has been a recent transition to a more outward-looking government and for many, the future for Ethiopia is looking brighter once again. There is much interest from the development community and investors as the country starts to industrialise and play an active part in global value chains.
As part of this recent evolution, Ethiopia, with the support of the World Bank and others, has invested in industrial parks with the aim of attracting garment manufacturers. This has been well publicised with a number of suppliers to major brands such as PVH and H&M producing there. Undeniably, one of the selling points has been the low cost of labour. This ‘cheap’ workforce is in part the result of Africa largely missing out on the globalisation of the late 20th Century (apart from the fresh produce industry) with the horn of Africa given a wide berth by many global brands. This has left Ethiopia and many African nations still sporting a large and relatively poor, rural population.
Therefore, if the textile industry can offer entry-level industrial jobs, this certainly has some potential value. In addition to the ready supply of low-cost labour, the Ethiopian government is actively taking steps to attract investment (by accommodating buyer requests and providing infrastructure and tax benefits, etc.) The aim is to move the country forward and put Ethiopia in pole position as a major African hub of the textile industry.
This also leaves Ethiopia to serve as a prime 21st Century test case to demonstrate what happens if the focus is on investment in the infrastructure, factories, logistics and business incentives without a corresponding investment in the policies, social infrastructure, social dialogue and worker representation that means jobs are not exploitative.
Some employers complain that workers don’t stay, or move around a lot from factory to factory, or that recruitment is difficult. On the other hand, some employees report that wages are low, workers are not treated well, basic facilities such as toilets and lunch spaces are not provided and, tragically, cases of sexual harassment and violence are going unchecked. We have seen this scenario in too many other countries where, for instance, a young rural woman will come for her first job in an industrial setting and is expected to work, often for long hours, without support or recourse when things go wrong. Such workers are dislocated from their community and vulnerable, unused to factory conditions or long hours, and may not have the support system in place or the confidence to speak up, which results in a bad experience for them and a bad reputation for the industry.
On my recent visit to Ethiopia, there was recognition among many I spoke to that there is a limited time to get things right before investment really takes off and unethical practices take hold as the norm. On a positive note, I am told that the industrial parks are well designed, the factory sheds are of a high standard, and the logistics are improving. However more needs to be done to ensure that workers enjoy decent standards of work, are paid a decent wage, are treated with respect and have the opportunity to join a union if they wish to. These principles must be embedded in the formative roots of labour practice and policy in the textile industry in Ethiopia. Getting this right now means that the country can sustain sector growth in the long-term, while also benefiting owners, workers, families and their communities.
With the chance to make positive social and economic investment choices from the ground up in one of Africa’s most promising industrial hubs, any brand or supplier considering investing in Ethiopia should ensure that they and their suppliers are fully aware of the situation in the country and invest not only in the environmental sustainability of their factories and raw materials, but in the people and communities who produce the clothes they will sell on to you and I.