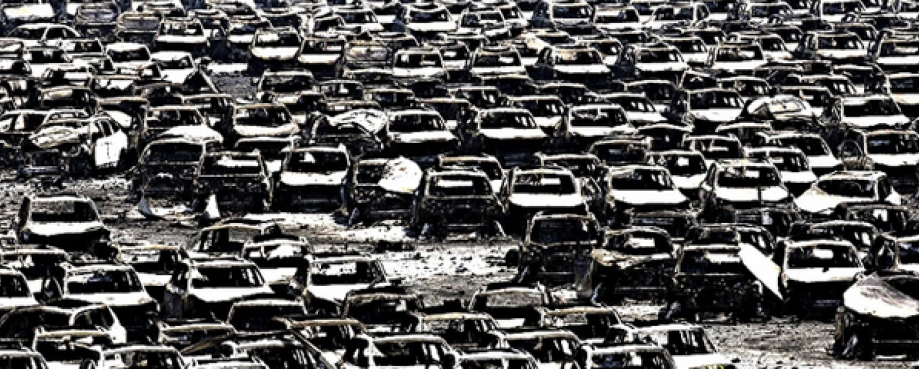
We may never know exactly what happened in Tianjin on 12 August when a massive chemical explosion killed 173 people. The Chinese government will probably blame it on corrupt officials, and several have already been arrested - including the head of the country’s Work Safety Agency.
But Tianjin is only different because of the scale. The excellent China Labour bulletin has an interactive map of accidents and they occur every day. So just two weeks after Tianjin, on 31 August, another chemical explosion took place in Shandong province killing 13 workers. A week earlier, a fireworks factory blew up in Hainan province.
So can work EVER be made safe in China? The short answer is yes. Two things are essential:
First, you need standards; and then you need a culture of implementation.
Let’s deal with standards first. A standard is a way of measuring. When we manage safety and health at work, we need standards. In the case of Tianjin, there should be a standard about the maximum quantity of a hazardous chemical that can be stored - sodium cyanide for example, which was one of the chemicals involved.
There should be a standard for the strength of the pressure vessel in which the chemical should be stored. Maybe there should be a maximum temperature at which it is stored, because if it exceeds this temperature, it may spontaneously combust. If there is, how is it achieved?
An important point to bear in mind is that a chemical does not change its chemical characteristics if it moves country. If you are storing sodium cyanide in China rather than the UK, it does not need storing at a higher temperature, or require a thinner gauge of metal in the tank where it is kept.
So, the standard should be the same anywhere in the world.
It is not correct to say “oh, well, we can’t demand the same standards in China as in the UK.” The chemical does not change - the danger it poses does not change, so why should the standard change?
Now this also applies to other standards. Let’s consider noise. We are asking questions like: “What level of noise is acceptable?” This is a bit personal for me, as my father was in the Royal Air Force in the war, and exposed to very high levels of noise on aircraft engines. He began to lose his hearing 30 years later.
Many hazards, like noise, have a long latency period - the damage only becomes apparent many years after exposure. A worker only starts having trouble breathing many years after working in a dusty environment. But there will be a standard that answers the question: “How much of this dust is it safe for a worker to breathe?”
Just like the chemical, a person’s lung do not really change when they are in a different country.
An Indian worker, or a Chinese worker, will go deaf if exposed to excessive noise over a prolonged period. Their lungs will scar with silicosis or pneumoconiosis if they work in an environment where they are exposed to the dusts that cause those diseases over a long period.
So we should be looking for the same standards for noise or dust exposure anywhere in the world, just as we would for storing large quantities of chemicals.
Actually, not quite. Most of the “safe” levels of chemical and dust for workers to breathe are taken from the US Conference of Government Industrial Hygienists (ACIGH) - despite its name, it is actually a non-governmental, scientific association. Every year, it publishes and updates guidelines known as Threshold Limit Values (TLVs) and Biological Exposure Indices (BEIs). They are a personal “safe” dose for a worker to breathe.
These are adopted around the world. And they are based on the average US male worker. Now I’m not being size-ist here. But US workers generally weigh a tad more than your average Chinese worker.
So the TLV and BEI should be lower for Asian workers.
That’s right. Exposure levels – for dusts and chemicals at least – should be lower in India and China.
The ACIGH revises the TLVs every year. The Indian government has not changed the TLVs since 1987. Indian workers, it seems, are very tough.
Anyway, you have a standard - there are several places to get them from. If you are stuck to find one, ask me nicely and I will point you in the right direction.
But let’s now turn to the second requirement for a safe China, or India, or wherever you are sourcing from: a culture of implementing the standard.
To make the point as clearly as possible: standards on their own will not improve safety and health at work.
Everybody has a role to play in implementing standards. The government needs to appoint sufficient labour inspectors, who are properly qualified and trained and empowered to go to workplaces, check the standards are being followed and prosecute if they are not.
We can be proud that the United Kingdom was the first country in the world to appoint labour inspectors - way back in 1833. As mentioned in a previous blog, this proposal was first raised by Robert Owen in his draft Factories Act of 1815. Just over a century later, the Treaty of Versailles included a clause that every country should have a system of factory inspectors. Yes, that’s right, the Treaty of Versailles that you thought was just about the end of the Great War, had a whole chapter in it about labour conditions.
But inspectors can’t be everywhere, so in the workplace the employer and the workers have to follow the standard themselves. That means safety officers, safety committees - even better safety representatives appointed by a trade union. That’s the system we have in the UK and it has been a major factor in our low work accident rates.
There needs to be, to use an overworked phrase, ownership of a safety standard and that can only come about when management are prepared to involve workers, and when workers have a voice. That is how you build a culture of implementation of a standard. And is not going to happen in China where the official trade union is subordinated to the Communist Party. Or those countries that don’t allow workers to organise.
Mind you, there is another map on the website of the China Labour Bulletin; it’s a strike map and it seems just as busy as the accident map.
It is a hopeful sign. Workers are taking action despite all the obstacles put in their way by the official trade unions, the party and the state.
Eventually, that might lead to a safer China.