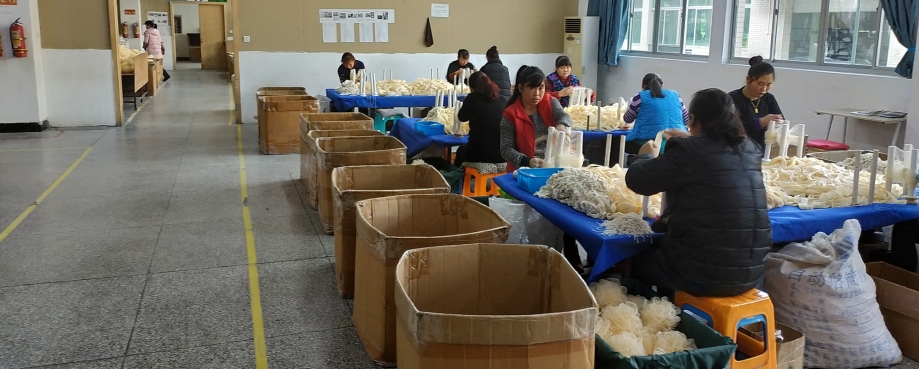
At the Netbridge factory, the owner Jason Sun’s office door is always open. And, when any workers want to discuss work-related issues or arrangements, Jason always listens with an open mind.
Factory owner Jason Sun explains why it’s important to talk. “It’s always good practice to meet in the middle and it helps with understanding each other. In this regard, communication goes two-ways.
“Sometimes management may overlook needs, but sometimes a request may not be reasonable. Nevertheless, I always hear what people want to say, and I will tell them what I think too,” Jason says.
Netbridge makes bath and knit products for The Body Shop at facilities in Taiwan and China. It’s China factory has been taking part in ILO SCORE training since 2018. SCORE is the ILO’s training and technical assistance programme that supports small and medium enterprises to increase productivity and improve working conditions.
Better and more regular communication
Better communication is seen as a starting point when implementing SCORE. In this current series, which is being jointly run with ETI, SCORE is helping to build a bridge between factory owners, management teams and workers on the shop floor. The aim is that everyone works together towards common interests and all benefit from the process.
With the help of SCORE trainers, who came to the Netbridge factory for onsite training, Jason organised weekly Enterprise Improvement Team (EIT) meetings. These discuss joint worker and manager concerns, and how to solve them – together.
In Netbridge’s case, the weekly meeting includes Jason (as the factory owner), two senior managers, two administrative staff members, and six supervisors from different production departments and two or three selected workers, on a rotation basis.
Workers are particularly encouraged to involve themselves in the discussion.
Complaint mechanism set up
From the first EIT meeting, the SCORE trainer helps an enterprise set up a complaint’s mechanism.
This is regarded as crucial, as it establishes a process that allows staff to air concerns formally, rather than let them fester. At the same time, it enables management to understand problems and try to solve them.
As part of the process, the mechanism encourages employees to put forward reasonable suggestions to a set formula:
- Critical areas for improvement are identified.
- ‘Need-to-improve’ issues are noted with a responsible person assigned.
- EIT team members jointly discuss how to creatively solve issues, with budgets, labor costs and time management in mind.
- Once an improvement plan is decided, the responsible person will take photos of the before and after, and this will be reviewed in subsequent meetings.
- A policy to carry out regular joint checks to review and evaluate progress is also implemented.
Continuous improvement
It was through the weekly meetings that Jason and the rest of Netbridge’s EIT members gradually started to develop an attitude of continually looking to implement improvement.
The factory has seen more effective output and a significant drop in defect rates.
According to statistics, small improved projects raised during EIT meetings in July 2018 were five in total. But by December 2018 these had increased six-fold to 33.
Likewise, problems related to health and safety decreased with the implementation of Module 5 of the training: "Safety and health as a platform for better productivity," which led to positive results in many aspects.
Jason recognizes that a safety-focused and caring culture not only benefits workers, but also the enterprise. It leads to a reduction in accident rates and consequently compensation costs. It also leads to better quality, reputation gains and greater staff commitment.
SCORE and the Chinese government:
Introduced to China in 2008, the ILO and Chinese government have jointly promoted the SCORE project. Jia Hongwei, China’s first expert trainer of SCORE, explains that the programme has won support at the national level of government. This includes the State Administration of Work Safety, the China Enterprise Confederation and the local enterprise federation.
During Phase II of implementation, SCORE China has established long-term relationships with the State Agency for Worker Safety (SAWS) and the Confederation of Chinese Enterprises (CEC) and is continually generating good results. “The reason why the Safety Supervision Bureau attaches great importance to the SCORE programme is that we provide the golden key to safety management. That is, SCORE truly enables employees to participate, to identify problems themselves, and to improve themselves,” says Jia.
Encouraging micro level efficiency
The objective of the SCORE safety module is to increase efficiency at the micro level by keeping the workplace neat, orderly and accessible.
It’s been proved that being neat and organised improves work performance.
Specifically, in Netbridge, defect rates in crucial production processes decreased from 10% in July 2018 to 3.2% in December. Defect rates in a component of the finished product also reduced from 2.5% to 1%.
Positive changes are everywhere. Information boards are in place and are being read. There’s also a first-aid kit, an evacuation map route and signposting throughout the factory – this includes warning signs of dangerous chemicals.
Netbridge also tidied up and reorganized its warehouse, which was considered to be too disorderly. The warehouse now has a fire safety pathway and all products and raw materials are clearly labelled.
These visually dramatic results have become a signal, encouraging workers to suggest initiatives that boost productivity.
Case study: replacing wood with plastic
Su Shehui, a warehouse manager who has worked for the factory since 2002, suggested replacing the wooden factory stock boards to plastic pallets. This allows all products stored in the warehouse to be lifted and transferred directly to shipping trucks, saving workers time and effort when downloading and uploading products. It also minimises the chances of back injuries. Su appreciates that SCORE has become a platform for workers to speak their mind and bring forward ideas. “While I had the idea a few years ago, there was no opportunity before to make my voice heard,” he says.
Harmonious working environment
Jia Hongwei confirms that SCORE’s aim is to break any mental barriers that exist between management and workers.
He says: “Let the boss directly hear what workers are thinking, and also let workers know what the boss has in mind.
“In the end, SCORE’s final goal is to create a harmonious working environment.
“The factory owner, managers and employees are all equally key to the success of each other. That means everyone must engage and communicate actively.”