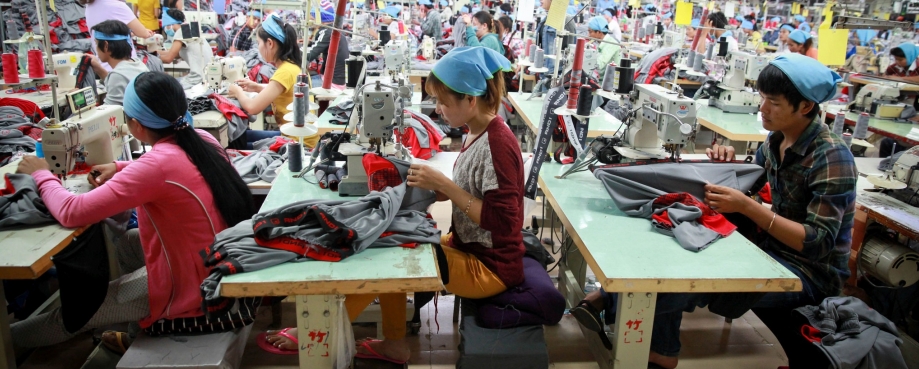
Triple whammy for garment workers
The thing about supply chains is that – like any other chain – when something happens at one end of it, there are reverberations all the way along the chain. And the people at the start of the chain, those who produce the raw materials and process them into goods for sale – are often the hardest hit.
Take the garment supply chain, for example. In February, garment factories in Myanmar started struggling to get fabric and accessories from China. The reason is now evident to the whole world.
But then came a second hit, this time from the other end of the chain. Buyers started cancelling orders. Within a short time, 40,000 to 50,000 garment workers had lost their jobs. The story was echoed across numerous garment producing countries, including Cambodia, where more than 60,000 workers lost their jobs as their factories closed as brands failed to pay in full for orders that had been completed or were in production.
And finally, a triple whammy, when governments imposed lockdowns, travel restrictions and quarantines to protect people from coronavirus; keeping people alive, but further hampering their ability to earn a living.
At an ETI-hosted webinar last week, Jacob Clere, of SMART Textile & Garments – a lobby group in Myanmar, and Piseth Duch, of the Pro Bono & Advisory Law Group in Cambodia, shared these sobering facts – as well as their suggestions for how brands could help.
Prevention is better than cure – but can be painful
Thankfully, neither Myanmar nor Cambodia have (yet) seen high coronavirus infections figures – at time of writing there were 120 confirmed cases in Myanmar and 122 in Cambodia. But while prevention may be better than cure (or worse), the measures to keep people safe from the virus are adding to the economic woes of garment workers.
For example, the Cambodian government issued a travel ban during the public holiday, effectively placing 30,000 workers who had returned home for the holiday under a 14 days mandatory quarantine. Unable to return to work they received no pay for that period.
When you are on a subsistence wage, a shock like this can push you over the edge. Piseth cited an Oxfam report that said Cambodia is likely to face another economic setback with thousands falling back below the poverty line.
And although there has not been an actual ban in Myanmar, travel is strongly discouraged, so – according to a rapid survey by SMART at the end of March - most workers said that when their factories closed they would remain in place in the hope of regaining their jobs.
Most of the 135 workers surveyed had only had one month of savings in the form of cash and jewellery. If their unemployment extends beyond a month, they will be reliant on legal severance payment, which, as long as factories are able to pay this, will enable them to survive for several months. After that, they have nothing. “So time is our biggest enemy” says Jacob, “as some workers got unemployed back in March and some of them will quickly get into desperate situation.”
Myanmar’s social security law was only passed in 2014 so there hasn’t been time to build up a sufficiently large social security fund to help the tens of thousands across multiple industries whose income has been decimated by coronavirus.
A dangerous balancing act for governments
Jacob reports that there is good dialogue between Myanmar’s social partners; the confederation of trade unions, the garment association and the Ministry of Labour, who are trying – like their counterparts all over the world - to “work together and sort out what is the best for the industry and for workers, and try to balance many challenging and complicated factors, preventing the spread of the disease in the country and against the terrible economic impacts…”.
Trade unions are also trying to balance health and income; Cambodian union members in some factories are reporting inadequate health and safety mechanisms, leaving workers fearful of contracting Covid-19 from colleagues returning from holidays. Union leaders themselves feel under increased threat of losing their jobs during the crisis, making it difficult for them to organise and defend workers’ rights. In Myanmar, too there is a fear that union members are being singled out when workforces are being reduced.
At the time of the webinar, there were also concerns about the possibility of the Cambodian government imposing a state of emergency, giving them power to restrict the movement and freedom of individuals. Despite criticism of the draft law from UN independent experts and international NGOs, about restrictions on human rights and fundamental freedoms of Cambodia people, the law has since been enacted.
Some help is on hand…
Jacob explained that the EU is offering Myanmar a 5 million Euro emergency fund, the Myan Ku Fund, for direct cash payment to garment industry workers who have lost their jobs permanently, temporarily or partially. They will distribute the money via the mobile money transfer app, “Wave money”. Jacob’s organisation, SMART, is working closely with the Minister of Labour to try to fill any gaps. Workers can apply for the fund through the Ministry of Labour, their managers or by contacting a SMART hotline. SMART has also started advertising the fund to factory managers through its website and newsletter.
The Cambodian government, Piseth told us, is offering tax breaks for 6 months to 1 year to businesses that can show evidence of significant impact from the pandemic crisis and of the partial withdrawal of ‘Everything But Arms’ – a duty-free, quota-free agreement with EU for all imports except arms. Although for factories without enough profit to survive, the tax break is cold comfort.
Cambodian factory workers on temporary suspension, will get $70 each; $40 from the government and $30 from their employer. And if a Myanmar factory is subject to quarantine restrictions, workers will be eligible for 60% of pay during this period.
The Cambodian government is also working with local banks and macro finance to ask for a delay in loan repayments from affected workers. Factories can also ask for a delay in paying their national social security fund contribution during the pandemic crisis.
The EU is also committing to providing a 67 million Euro grant to help the Cambodian government to respond the pandemic, but on the other hand, the uncertainty triggered by the crisis will be exacerbated by the partial withdrawal of EBA.
What brands can do
“The best thing buyers can do is to honor all the contracts.” Says Jacob, a sentiment strongly echoed by Piseth. And the same would apply, in fact, to all contracts in every sector. That is, after all, the purpose of a contract and a fundamental tenet of responsible purchasing.
Jacob also recommended that brands provide clarity on future contracts, even if these will be at lower volumes, to keep the factory from folding.
ETI members can monitor that legal severance payments are made when workers are terminated, and that factories gained formal permission for suspending operation so that their workers are eligible for government benefits.
Finally, brands could consider contributing to relief funds for laid-off workers. Piseth described how some brands have set up emergency funding for relief responses for workers, including medical suppliers, PPE and food.
Solidarity and collaboration
“We understand it is difficult time for anyone including retailers,” says Jacob, “but I do think everyone in the industry should work together and the suppliers shouldn’t be get abandoned during this time.”
Piseth agrees; “Global response and solidarity and collaboration among brands is really needed in this crisis. For example joint relief and humanitarian efforts to address the urgent needs for supply chain workers.
After all, if we allow the links at the base of the supply chain to be smashed by this crisis – the reverberations will be felt not only by thousands of destitute garment workers, but all the way along the chain right up to the brands themselves.
A case in point: a factory in Myanmar that produces for the American market have had very uncertain orders for the beginning of May and only tentative long term orders from July. They fear they could collapse without support as they are unable to cover the workers’ salaries. If that happens, not only will their 700 workers become unemployed, but that supplier will no longer be available for the buyer.